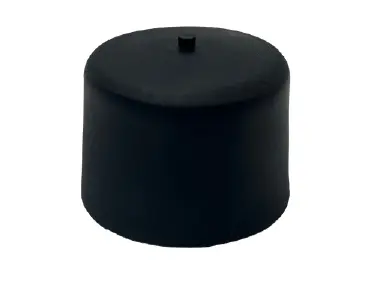
The Class 1B design utilizes a rectangular shape bead around the entire circumference of its mounting edge allowing the flange bead to be clamped inside the cylinder bore. This design offers a minimum outside housing diameter which is slightly larger than the diaphragm cylinder bore.
In some cases, this design eliminates the need for flange bolts or flange studs. It requires no bolt holes or perforations through the flange of the diaphragm.
Inversion of the piston corner radius is required to form the convolution. In order to retain the piston corner radius and prevent it from returning to its “as molded” shape, a curved lip retainer is recommended.
Because the Class 1B design provides for clamping the flange bead inside of the cylinder bore, the stroke capability is normally limited to the half-stroke in the SB direction only.
The cross-sectional area of the groove for retaining the bead should be equal to the cross-sectional area of the Bellofram bead itself. The corners of the groove should be machined square with minimum fillets. These practices are recommended to provide best retention of the bead. Elastomers are not compressible, and if the groove area is too small, it will definitely damage the rolling diaphragm.
It is recommended this design be used where differential pressures do not exceed 150 psi.