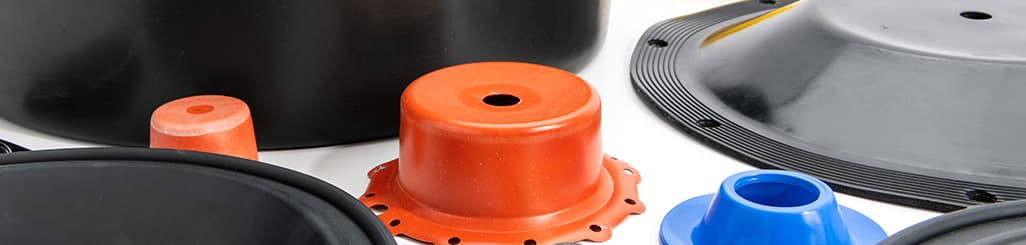
Articles and News
What Is Neoprene: Everything You Need To Know
Neoprene NTK Guide
In this guide, we will share everything you need to know about neoprene, a versatile and high-performance synthetic rubber. This article will provide valuable insights into neoprene manufacturing, its physical properties, and how it stacks up against other elastomers. Understanding these things will help you make informed decisions for your specific applications. Let’s begin by exploring neoprene and its unique properties.
What is Neoprene?
You may find yourself asking, “what is neoprene rubber?” Neoprene, also known as polychloroprene, is a widely-used synthetic rubber renowned for its versatility in various industries. Made from chloroprene monomer units, neoprene is polymerized into a stable and durable neoprene material with unique characteristics.
One of the key features of neoprene is its exceptional resistance to weathering, ozone, and chemicals, making it ideal for outdoor and harsh environments. Its remarkable flexibility allows it to endure repeated bending, stretching, and compression without losing integrity. These attributes make neoprene highly sought after in numerous applications. In the automotive industry, neoprene is used to create gaskets, hoses, and seals due to its excellent resistance to oil, fuel, and heat. The marine industry relies on neoprene for wetsuits, gloves, and diving equipment, thanks to its buoyancy, insulation, and water resistance. Neoprene also finds extensive use in construction, electrical, and medical fields, where its durability, electrical insulation, and resistance to aging are highly valued.
How is Neoprene Produced?
Understanding the neoprene manufacturing process provides insights into its unique properties and applications. Neoprene is produced through a series of precise steps that transform raw materials into the final neoprene rubber product.
As a neoprene manufacturer, our process begins with the selection and preparation of raw materials. The main ingredient is chloroprene monomer, derived from petroleum, along with various additives to enhance performance. These materials are mixed in a controlled environment to create a polymerization mixture.
The polymerization reaction bonds chloroprene monomer molecules into long chains, forming neoprene rubber. Post-polymerization, the neoprene undergoes processes like washing, filtration, and drying to remove impurities and improve physical properties. It is then formed into neoprene sheets, rolls, or other shapes through calendering or extrusion.
Quality control checks ensure the neoprene meets required specifications and standards. This includes testing mechanical properties, chemical resistance, and durability. The result is a high-quality neoprene material widely used in automotive, marine, sporting goods, and industrial sectors.
Mechanical Properties of Neoprene
Neoprene is celebrated for its exceptional mechanical properties, making it a preferred choice for various applications. Its strength, elasticity, and flexibility are key characteristics.
Neoprene exhibits excellent durability and resistance to wear and tear, withstanding high levels of stress and strain without losing structural integrity. This makes it ideal for applications requiring strength, such as gaskets, seals, and industrial belts.
Its high elasticity allows neoprene to stretch and return to its original shape without permanent deformation, beneficial in absorbing shocks or vibrations in applications like shock mounts and automotive suspension systems.
Neoprene’s flexibility enables it to be easily molded and shaped into various forms, allowing manufacturers to create custom cut neoprene designs. This flexibility also provides a tight, secure fit in sealing applications. Neoprene is resistant to heat, chemicals, and weathering, making it suitable for both high and low-temperature applications. It withstands a wide range of chemicals, including oils, solvents, acids, and alkalis, and exhibits excellent weather resistance, ensuring longevity even in harsh conditions.
The mechanical properties of neoprene foam make it an excellent choice for demanding environments in industries such as automotive, construction, marine, and sports equipment manufacturing.
Neoprene vs. Other Elastomers
Neoprene uses vary based on the application. Choosing the right elastomer for your project requires understanding the key differences between various materials. Here, we compare neoprene with two popular elastomers: EPDM and silicone.
Neoprene vs EPDM
Neoprene offers excellent resistance to weathering, ozone, and chemicals, making it a versatile synthetic rubber for applications requiring durability and flexibility. EPDM (ethylene propylene diene monomer) is renowned for its outstanding resistance to heat, weather, and aging, often chosen for outdoor applications exposed to harsh environments.
When comparing neoprene and EPDM, consider your project’s specific requirements. Neoprene is typically preferred for its oil and water resistance, while EPDM excels with its durability and high tensile strength. Additionally, neoprene has better resistance to flame and high temperatures compared to EPDM.
Neoprene vs Rubber
Silicone rubber, another popular elastomer, offers excellent resistance to extreme temperatures, UV radiation, and aging, making it suitable for applications requiring high thermal stability and excellent electrical insulation properties. However, neoprene outperforms silicone in oil and solvent resistance.
Selecting the right elastomer depends on several factors, including operating conditions, temperature range, chemical exposure, and mechanical requirements. Assessing these factors ensures optimal performance and longevity for your application. Our team at Bellofram Elastomers is always here to assist you in selecting the right elastomer for your needs.
Benefits of Choosing Bellofram Elastomers
At Bellofram Elastomers, we pride ourselves on offering premium performance, custom solutions, and export support. Our products are engineered to meet the highest standards, ensuring reliability in extreme environments.
Working with us provides several benefits:
Premium Performance: Our products are designed for durability, flexibility, and resistance to harsh conditions, ensuring they perform reliably in demanding applications.
Custom Solutions: We understand that every project has unique requirements. Our team works closely with you to develop tailored solutions that meet your specific needs.
Export Support: We offer comprehensive export support, ensuring our high-quality products are available to customers worldwide.
There are several neoprene manufacturers in the U.S., but in choosing Bellofram Elastomers you gain access to a single-source provider that reduces complexity and lead times. Our scalable production capabilities allow us to support both small prototypes and large-scale manufacturing, providing the precision, reliability, and efficiency you need for project success.
Contact us today to learn more about our neoprene or other elastomer products and how we can help you achieve your project goals.
If you found this information helpful and would like a PDF copy, you can download it here.