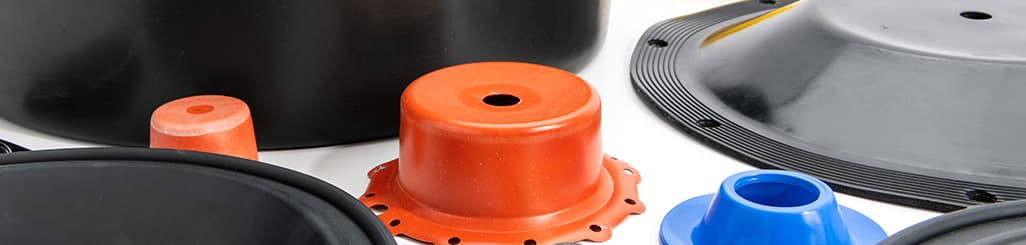
Articles and News
Comparing EPDM vs. Silicone
Comparative guide to explore the differences between EPDM and Silicone
In this guide, we will delve into the key differences between EPDM and Silicone Rubber, two of the most widely used elastomers in various industries. Understanding these differences will help you make informed decisions for your specific applications. Let’s begin by exploring what EPDM is and its unique properties.
What is EPDM rubber?
What does EPDM stand for? EPDM stands for Ethylene Propylene Diene Monomer. It’s a synthetic rubber known for its exceptional versatility and resilience. As an EPDM manufacturer, we understand the importance of materials that can withstand harsh environmental conditions. EPDM rubber excels in weather resistance, offering outstanding durability against ozone, UV rays, and extreme temperatures. Its physical properties make it an excellent choice for the automotive and construction industries as well as other outdoor applications.
EPDM’s popularity stems from its high tensile strength, impressive elongation, and remarkable flexibility, which allow it to endure repeated stretching and bending without compromising its integrity. This elastomer also boasts superior resistance to water and steam, making it ideal for sealing and gasket applications where maintaining a tight seal is critical.
At Bellofram Elastomers, we’ve ramped up our EPDM manufacturing to offer a wide range of EPDM products tailored to meet your specific needs. Our EPDM materials, including EPDM foam rubber and EPDM sponge rubber, are manufactured using advanced technology and strict quality control processes, ensuring exceptional performance and durability. Whether you need EPDM sheets, gaskets, seals, or custom EPDM products, our team of experts is ready to provide reliable solutions.
What is Silicone rubber?
Silicone rubber is a highly versatile elastomer known for its unique properties and wide range of applications. Composed of silicon, oxygen, carbon, and hydrogen, silicone rubber stands out for its excellent stability, high temperature resistance, and flexibility, making it suitable for numerous industries.
One of the most significant advantages of silicone rubber is its exceptional temperature resistance. It can endure extreme temperatures, from as low as -60°F to as high as 390°F, without losing its physical properties. This makes silicone rubber ideal for applications involving exposure to extreme heat or cold.
Silicone rubber also excels in electrical insulation, boasting high dielectric strength and low electrical conductivity. These properties make it a preferred material for electrical and electronic applications.
Another notable feature of silicone rubber is its excellent weatherability. It is highly resistant to UV radiation, ozone, and harsh weather conditions, maintaining its performance even in demanding outdoor environments. Furthermore, silicone rubber has good chemical resistance, allowing it to withstand exposure to various chemicals, acids, and alkalis without significant degradation.
Overall, silicone rubber is a versatile elastomer that offers a combination of unique properties, including temperature resistance, electrical insulation, weatherability, and chemical resistance. Its applications range from automotive components and seals to medical devices and consumer electronics.
EPDM vs Silicone (EPDM vs Rubber)
EPDM and Silicone Rubber are both popular elastomers used across various industries, and both silicone and EPDM rubber uses are endless, but they differ in several key aspects. Understanding these differences can help you choose the right material for your specific needs.
General Characteristics: EPDM is renowned for its superior weather resistance, making it ideal for outdoor applications. EPDM UV resistance is high as it offers excellent resistance to UV rays, ozone, and harsh weather conditions. Silicone rubber, on the other hand, offers extreme heat resistance and sterile properties.
Temperature Range: EPDM can handle temperatures ranging from -40°F to +250°F, whereas silicone rubber can endure a wider range, from -60°F to +390°F. This makes silicone rubber more suitable for applications involving extreme heat or cold.
Elongation and Flexibility: Silicone rubber has a higher elongation at break, providing greater flexibility and making it suitable for applications requiring significant movement. EPDM, while less flexible, has better tear strength, improving its durability and making it more resistant to tearing or ripping.
Choosing the right material is crucial for the success of your project. Consider the specific requirements of your application, including temperature range, elongation, oil resistance, environmental resistance, and tear strength. By selecting the appropriate elastomer, such as EPDM or Silicone Rubber, you can ensure optimal performance and longevity.
Benefits of Choosing Bellofram Elastomers
At Bellofram Elastomers, we pride ourselves on offering premium performance, custom solutions, and export support. Our products are engineered to meet the highest standards, ensuring reliability in extreme environments.
Working with us provides several benefits:
Premium Performance: Our products are designed for durability, flexibility, and resistance to harsh conditions, ensuring they perform reliably in demanding applications.
Custom Solutions: We understand that every project has unique requirements. Our team works closely with you to develop tailored solutions that meet your specific needs.
Export Support: We offer comprehensive export support, ensuring our high-quality products are available to customers worldwide.
By choosing Bellofram Elastomers, you gain access to a single-source provider that reduces complexity and lead times. Our scalable production capabilities allow us to support both small prototypes and large-scale manufacturing, providing the precision, reliability, and efficiency you need for project success.
Contact us today to learn more about our EPDM or other elastomer products and how we can help you achieve your project goals.
If you found this information helpful and would like a PDF copy, you can download it here.